In this article, we will discuss the various types of Sheet Metal Operations. But before moving ahead to understand these operations, we should also understand what actually sheet metal is.
Sheet Metal: Sheet Metal is a thin sheet produced by rolling or hammering. These thin sheets are used to produce various types of sheet metal products by a sheet metal manufacturer according to requirements. The thickness of the sheet metal ranges from 0.15mm to 6 mm. Above 6mm, the sheet is not called sheet metal. It is called a plate. And, below 0.15mm, the sheet is called a foil.
Also Read: Sheet Metal Fabrication Process [Step-By-Step Explained]
Table of Contents
Types of Sheet Metal Operations:
The sheet metal operations are of the following Types:
- Bending Operation
- Shearing Operation
- Blanking Operation
- Punching Operation
- Piercing Operation
- Trimming Operation
- Drawing Operation
- Embossing Operation
- Squeezing operations
Bending Operations are further of the following types:
- Channel Bending
- U-Bending
- V-Bending
- Offset Bending
- Edge Bending
All of these types of operations are explained below in detail:
1) Bending Operations:
The metal forming processes, in which a sheet metal piece is caused to bend and get formed in the desired shape by the application of a force, are called Bending Operations. The types of bending operations are explained as follows:
Channel Bending:
In this type of bending, there is a die of channel shape and also a punch according to the shape of the die.
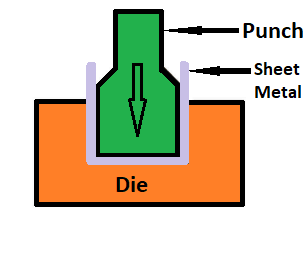
As shown in the above image, the sheet metal piece is placed in between the die and punch. When a force is applied to the punch to move into the die, the sheet metal piece, in between, gets the shape according to the shape of the die and punch (i.e., a channel shape).
U-Bending:
In this bending operation, there is a die of U-shape and the punch is also according to that as shown in the image given below:
When the punch is pressed by a force to move into the die, the sheet metal piece (in between the die and punch) gets formed in a U-shape.
V-Bending:
In the V-Bending operation, the die and punch are according to V-shape, as shown in the image given above. In this kind of sheet metal operation also, when the sheet metal piece is pressed between the die and punch; it gets formed into the shape of the die i.e. V-shape.
Offset Bending:
In this type of bending operation, the sheet metal piece is formed in an offset shape.
As shown in the image given above, the punch and die are also according to this shape so that the sheet metal piece can be formed into the desired shape.
Edge Bending:
In edge bending operation, an edge of the sheet metal piece is bent. In this operation, the sheet metal piece is fixed or held in between two dies from one end, as shown in the above image. Then a punch is forced to strike upon the other end which is free (or unfixed). Thus the open/unfixed edge of the sheet metal piece is bent to complete the forming process.
2) Shearing Operation
Shearing is the metal-forming process in which a sheet metal piece is separated into two parts.
In this, the sheet metal piece is placed or held in between two dies from one end (as shown in the image above). And, the punch is impacted on the other end of the sheet, causing the shearing effect. Thus the piece is divided into two parts.
3) Blanking Operation
In this type of sheet metal operation, small piece/pieces of a circular shape or any other shape are sheared from the center of a large piece of sheet metal.
In this, the small piece that comes out is called a Blank (desired product) and the remaining material in the large piece (after blanking) is called scrap, as shown above. A Punch and a Die is used for this blanking operation.
4) Punching Operation
Punching is also an operation just like Blanking. But the main difference is that the Blank piece which was the desired product in blanking is the scrap here in the punching operation. And, the remaining material which was the scrap in blanking is the final/desired product in this punching operation, as shown in the image given below.
So it is just the opposite of Blanking but the process is almost the same. Punch and die are also used here just like blanking operation.
5) Piercing Operation
Piercing is the operation in which very small holes are created in the sheet metal piece without removing any material from the sheet or by removing a very small quantity of material (shown below in the image).
Punch & die both are used even in this process. The punch used in the Piercing operation is generally of bullet shape.
6) Trimming Operation
Trimming is the operation that involves creating complex shapes or intricate designs in small objects. Excess metal is shredded off to make final designs.
7) Embossing Operation
Embossing creates raised surfaces or indentations like alphabets, numbers, etc., on metal sheets. The thickness of the metal sheet remains unchanged, and changes and textures are seen.
8) Drawing Operation
Drawing is a technique that produces metal products shaped like vessels, cylinders, and hallows. Deep drawing makes cylinders with a larger width, and shallow drawing makes vessels with a smaller width.
9) Squeezing Operation
The squeezing is used to alter the thickness of the metal, generally ductile metals. Thick metals are easily changed to get a slimmer size.
So I hope this article has made a comprehensive explanation of various sheet metal operations in a detailed way.
I also recommend you to read the articles whose links are given below: